АО «Воткинский завод». г.Воткинск.
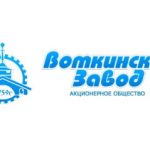
Воткинский завод – одно из старейших предприятий России, градообразующее предприятие города Воткинска, Удмуртская Республика, основанное в 1759 году.
В настоящее время одно из предприятий на основе Воткинского завода выпускает межконтинентальные ракеты стратегического назначения «Тополь-М», являющиеся основой ядерного щита России, и ряд других изделий военного назначения. Среди гражданской продукции — оборудование для нефтяной, газовой промышленности и станки.
Сайт компании: https://vzavod.ru
В Акционерном обществе «Воткинский завод», одном из крупнейших предприятий Корпорации «Московский институт теплотехники», реализован проект внедрения автоматизированной системы «Управление производством» на базе программного продукта отечественной разработки КСУ «Парус».
Основная цель проекта — создание единого информационного пространства.
Первый внедренный модуль системы «ПАРУС» — «Управление закупками, складом и реализацией» эксплуатируется на предприятии с 2003 года. Затем были внедрены «Бухгалтерский учет», «Управление персоналом и штатное расписание» и «Расчет заработной платы».
В 2012 году стартовал этап автоматизации учета и планирования производства — ключевой для машиностроительных предприятий, который направлен на:
- повышение качества выпускаемой продукции;
- сокращение сроков подготовки производства;
- снижение непроизводительных расходов;
- повышение эффективности производства;
- создание инструментов контроля за ходом производства.
ПП «ПАРУС – Предприятие 8» внедрена в 30 цехах основного и вспомогательного производства система внутри- и межцехового учета ДСЕ (деталей и сборочных единиц). К системе «ПАРУС» подключены подразделения снабжения, маркетинга, планово-экономический и юридический отделы, бухгалтерия, складское хозяйство, производственный отдел, цеха основного и вспомогательного производства. Общее количество пользователей системы «ПАРУС» на предприятии — около 2500.
Внедрена система внутри- и межцехового партионного учета ДСЕ в цехах основного и вспомогательного производства. Партии деталей запускаются в производство на основании подетального плана, рассчитанного с учетом плана выпуска изделий и заключенных договоров. Движение ДСЕ сопровождается электронными сдаточными накладными, что позволяет контролировать местонахождение ДСЕ в любой момент времени, четко верстать планы и осуществлять оперативный контроль их выполнения.
Внедрена система учета труда производственных рабочих, позволяющая составлять сменно–суточные задания рабочим и оформлять единые рабочие наряды на оплату труда.
Разработана система сертификационного учета материалов. Она позволяет вести учет получаемых материалов в разрезе сертификатов завода-изготовителя, сертификатов складского хозяйства и цеховых сертификатов, также в системе ведется учет проведенных испытаний, заключений о допуске материала в производство.
Система в режиме реального времени обеспечивает контроль выполнения ГОЗ на всех этапах производства, использование ресурсов предприятия, в том числе загрузки производственных рабочих и оборудования.
Руководство предприятия своевременно, в режиме online, имеет возможность получать достоверную информацию, необходимую для принятия эффективных управленческих решений. Проводится мониторинг деятельности предприятия на основе отчетов о поступлении продукции на склад, о ходе производства, заключенных договорах и их исполнении, сформированных и выполненных заказах, изготовленных ДСЕ и т. д.
В результате проекта снизилась трудоемкость бизнес- процессов и повысилось качество информации. Так например, на предприятии за месяц формируется порядка 20 тысяч межцеховых сдаточных накладных, которые в прошлом оформлялись вручную, а затем перфорировались операторами в систему, в настоящий момент они создаются в электронном виде с использованием НСИ (нормативно справочная информация).